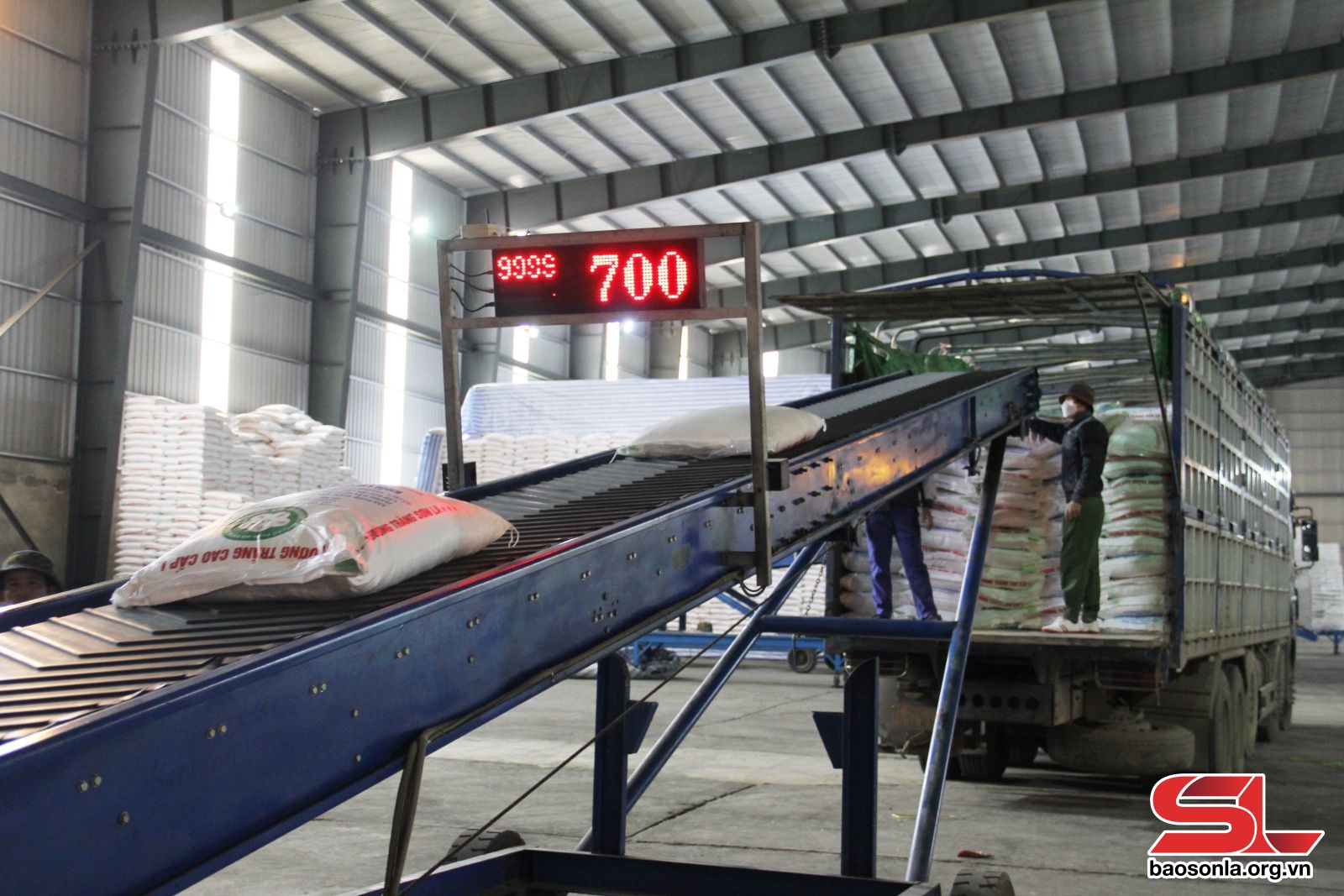
A typical example in this effort is the Son La Sugar Joint Stock Company. Since 2018, it has invested tens of billions of Vietnamese dong in upgrading its processing lines; promoted the application of modern technology to stabilise the capacity of nearly 5,000 tonnes of sugarcane per day. In particular, the sugarcane preparation stage is completely replaced with new equipment and modern technology from India to increase the sugarcane preparation coefficient and reduce sugar loss through bagasse. The press machine system is bought from Ulka, India's leading press machine manufacturer, to achieve capacity and performance as expected. The stages of sugar refining and crystallization are also made with new, automatic technology, resulting in effective production. To date, the factory has automated 40% of its production process, ensuring that the processing lines consume all raw sugarcane provided by farmers in the harvest season. The factory strives to complete its purchasing, production and processing plans for the 2023-2024 sugarcane crop in April 2024.
The Doveco Son La Vegetable and Fruit Processing Center is a complex of agricultural product processing factories using modern technology lines from Italy, Japan and China, with a total capacity of 52,000 tonnes of products per year, including frozen production lines with capacity of 20,000 tonnes per year; canning lines with capacity of 20,000 tonnes per year; and drying lines with capacity of 12,000 tonnes per year. The entire machinery system uses modern technology. The lines, when operating, support and complement each other, creating products with diverse designs and perfect quality, meeting market requirements.
Businesses producing construction materials have even paid greater attention to automation in production to reduce labour and ensure safety for workers. In 2012, the Mai Son Cement Joint Stock Company was established and put into operation, installing the most advanced and modern production line with a European automatic control system. The product manufacturing process is monitored via a camera system connected to the central control room. Each production stage needs only 1-2 workers on duty and many workers are only needed in the final stage to directly load products from conveyor belts onto vehicles.
Currently, almost all cement production stages at the factory are automated and the production process is controlled through a computer system. Automation in production has contributed to improving product quality, bringing in higher economic efficiency. This year, the cement consumption has seen many advantages. Since the beginning of the year, more than 400,000 tonnes of cement and clinker have been sold. The company's 2023 revenue is estimated at about 300 billion VND (12.37 million USD).
Boldly applying new advanced techniques in production, many businesses have invested in modern machinery systems, automating partial or full production for improved production efficiency, contributing to increasing revenue, reducing costs and minimizing emissions, towards sustainable production and greening in production.
You have 500/500 characters left
Please enter 5 or more characters!!!