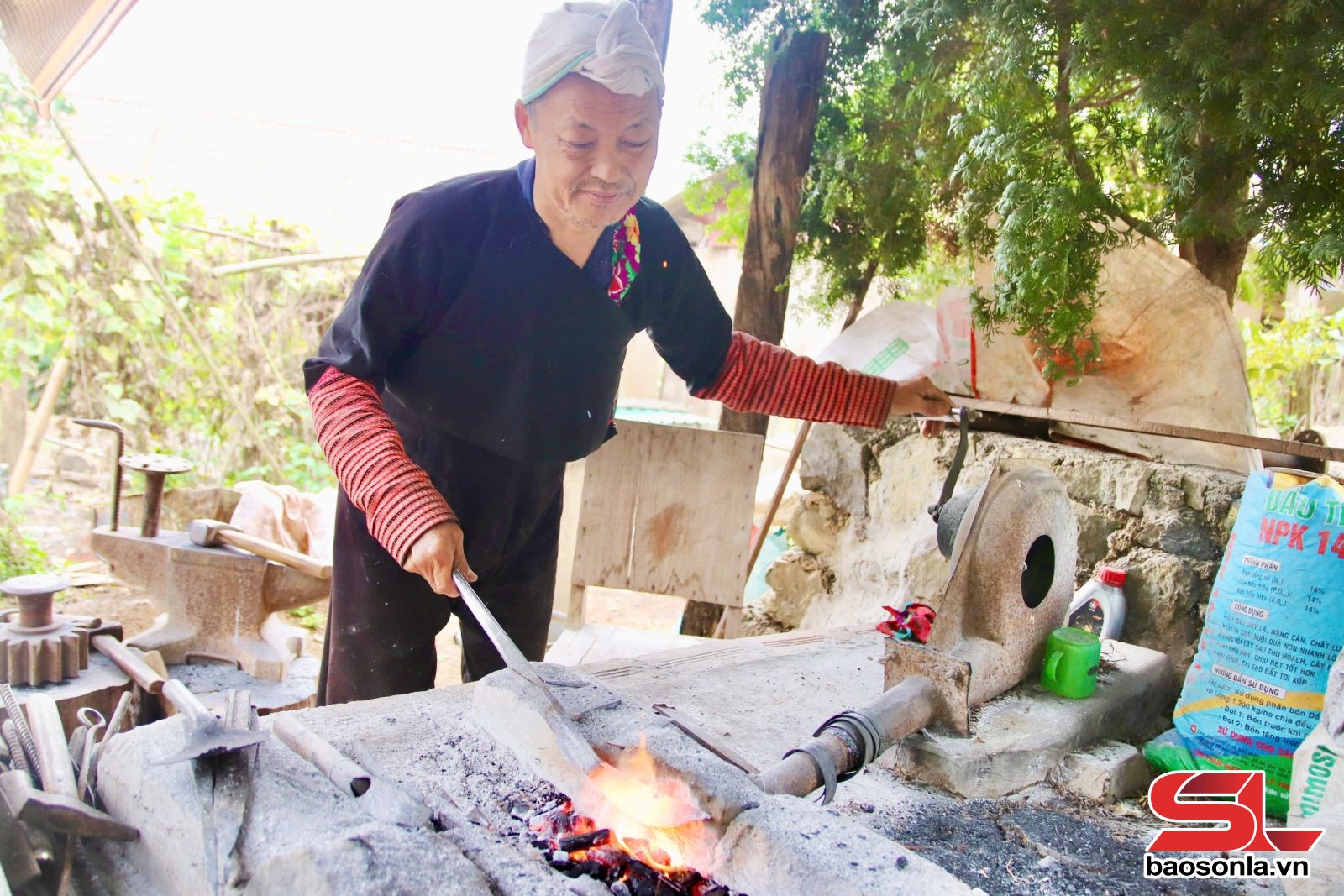
In Ta So 1 hamlet, Hang A Su has been a blacksmith for more than 60 years—longer than anyone else in the community. Despite his age, the rhythmic clang of his hammer remains firm and powerful. His handcrafted knives, hoes, and shovels are not only durable and sharp but also bear a unique craftsmanship that makes them highly sought after by locals and visitors alike.
“To create a high-quality forged product, a blacksmith must go through meticulous steps,” Su said. “From preparing raw materials, cutting iron, heating, shaping, tempering, sharpening, to fitting handles and making protective sheaths for knives, every stage requires skill and patience.”
Though simple in design, a traditional forge of the Mong people is fully functional. Built from stone and clay with wooden reinforcements, it houses a horizontal bellows made from a hollowed-out tree trunk. Inside, a piston lined with chicken feathers generates strong air currents, keeping the fire blazing hot for the forging process. Essential tools—including hammers, tongs, sharpening stones, iron anvils, water basins, fresh banana tree trunks, and charcoal—are all used to shape each piece with precision.
Most of the raw materials come from repurposed scrap metal. Depending on the tool, blacksmiths carefully select the appropriate steel. For sickles, machetes, and axes, they often use car suspension springs, coils, or construction steel—metals known for their flexibility, rust resistance, and long-lasting sharpness.
.jpg)
Blacksmithing is more than just physical labour as it demands skill, patience, creativity, and, above all, passion. Every tool is meticulously handcrafted, a testament to the dedication and craftsmanship of the blacksmith. As a result, traditional forged knives and farming tools often cost two to three times more than mass-produced industrial alternatives.
“I started learning blacksmithing when I was 15,” said Su. “It has been passed down through three generations in my family, from my grandfather to my father, and now to me. It’s tough, exhausting work with little financial reward, which is why many young people are no longer interested in. But I am committed to teaching my children and grandchildren, hoping they will continue this tradition and keep our family’s forge burning.”
The challenge of preserving the craft is evident in Ta So 1 hamlet. According to hamlet chief and secretary of the hamlet Party cell Mua A Di, the hamlet is home to 197 households and over 1,000 residents, all of whom are Mong people. “In the past, almost every family had a forge,” he said. “Now, only three remain. The younger generation is losing interest, putting the tradition at risk.”
To combat this decline, local authorities are encouraging younger residents to learn the craft. During summer holidays, children are brought to the forges to observe and gradually absorb the skills passed down through generations. Meanwhile, Moc Chau township is integrating blacksmithing into its community tourism strategy, transforming traditional forges into cultural experiences for visitors.
So far this year, the hamlet has welcomed over 3,000 tourists, generating approximately 300 million VND (12,000 USD). Beyond providing additional income for locals, these efforts are helping to preserve their heritage, including the traditional art of blacksmithing, ensuring that the flames never die out.
You have 500/500 characters left
Please enter 5 or more characters!!!